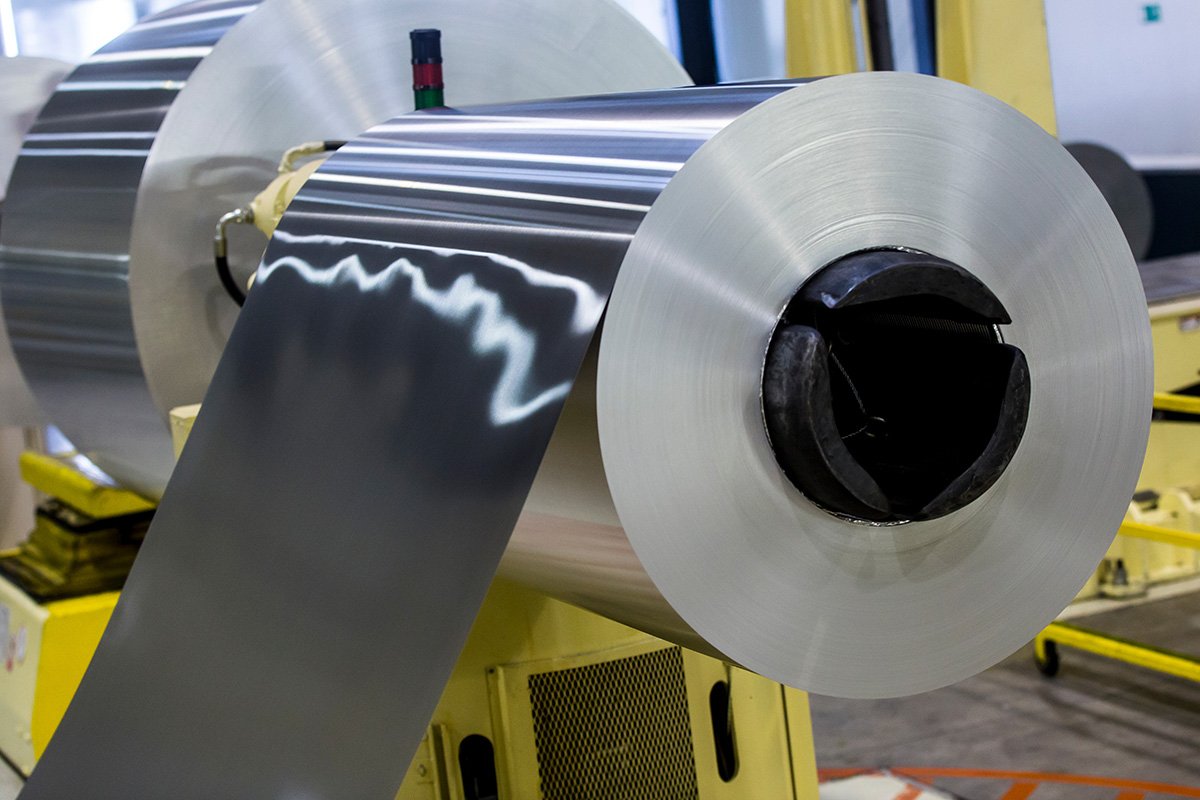
Coil Coating
Industry Overview
For over 43 years, Epcon has been the Oven and Oxidizer supplier of choice by the industry’s leading coil coaters. Widely recognized as the most efficient and cost-effective way to pre-paint steel and aluminum substrates, coil coating is a continuous and automated process for coating pre-fabricated metal. The various drying and curing ovens can be integrated with the air pollution control system via heat recovery methods to form a closed loop process. By harnessing the thermal energy released from destroying the VOCs emissions released during painting and coating application and curing, and then recycling that heat back to the coating line ovens, is not only a net zero solution, but also saves in operating fuel by allowing the oven burners to the completely shut off during continuous production.
Epcon has built or refurbished hundreds of Ovens and Oxidizers for the Coil Coating industry all over the world for companies in Russia, Saudi Arabia, Argentina, China, India and Singapore and others.
Many of the patented and proprietary technologies developed by Epcon were driven by the need to address unique challenges faced by Coil Coaters. Understanding the demands of metal coil coating industry comes from year of experience innovating with leading producers to develop highly engineered, state of the art technology. Epcon is proud to supply and service the most cost effective environmentally sound coil coating lines around the world.
Epcon’s personnel have vast experience in designing and building Ovens and Oxidizers and combination systems for the Coil Coating Lines, including High Pressure Hot Water Heat Exchanger systems for Wet Sections (Washlines).
To learn more about our robust history with Coil Coating projects and the latest evolution of Epcon’s integrated Combination Oven/Oxidizer systems please see our relevant case studies as well as our publication features. These projects highlight how our proprietary technologies allow leading coated coil producers to meet their quality, throughput capacity and energy efficiency goals – all within budget.