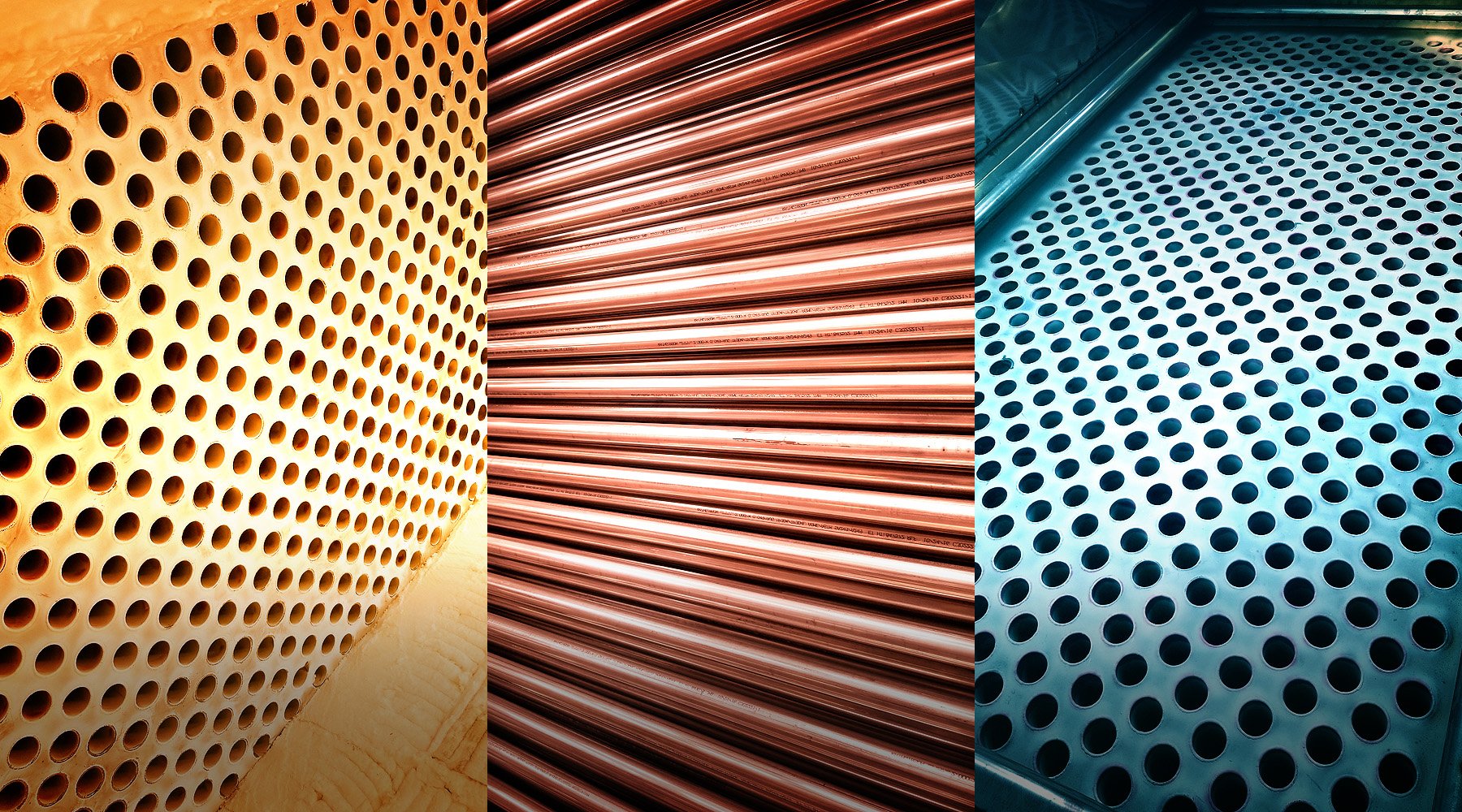
EPCON Products
Heat Recovery Systems

Heat Recovery Systems Quick Links:
Epcon: Leading Industrial Manufacturer of Heat Recovery Systems
Epcon has been designing and manufacturing custom heat recovery methods since our founding since 1977. These consist of both combining process heating operations with air pollution control systems, as well as multistage heat recovery.
The integrated “Oven/Oxidizer Combination” design with multistage heat recovery though heat exchangers is what sets apart Epcon from other industrial suppliers. With thousands of patented systems proven across multiple installations around the globe, we have saved our customers millions in operating cost.
We utilize various types of Heat Exchangers for transferring heat in the process, making use of thermal energy which would otherwise be wasted. In systems manufactured at Epcon, heat exchangers are used for pre-heating the process gas as it enters the thermal oxidizer, also called primary heat exchanger. These are typically in the form of regenerative and recuperative thermal oxidizers and economizers. From there secondary heating systems, via thermal fluid heaters such as waste heat hot water heaters and waste heat boilers, the thermal energy is further recycled through the as for heating of the manufacturing facilities and heating boilers.
Multistage Heat recovery in an integrated systems can create a closed loop system and is the best way to maximize your process efficiencies. Based on the unique process and requirements, different types of heat exchangers can be integrated into the overall system. Epcon hold several patents in the field of heat recovery and our team of experienced engineers can advise of the many opportunities to best utilize primary, secondary, and even tertiary heat recovery methods into your process operations. By extracting and recycling the thermal energy at various stages in the process, heat recovery not only saves on operating cost but also fuel efficiency.
Before shipment of the systems to customers, Epcon’s team conducts a full controls test, adjusting specialized tuning based on required set point temperatures and a particular range of process variables, to not only ensure the performance of the process heating equipment, but also confirm the desired Destruction Rate Efficiency (DRE) levels are met and process VOCs are destroyed.
In addition, once installed, our commissioning teams work with the integrated process heating and air pollution control system in operation to ensure all targets are precisely met in the field. Together the design of the air management system, PLC, remote sensors, and custom programming results in an integrated solution that delivers an easy-to-manage and integrated system controls.
The thermal recycling and heat recovery methods in a custom engineered systems that manage the airflow throughout the process translate to reduced energy costs, while enhancing emission compliance and performance. Our team not only has in-depth knowledge about the products, but also about the industries and applications to deliver quality performance that will exceed expectations.
Get in touch to get quotes for an integrated system by adding heat recovery technologies and methods into your customized process heating & air pollution control Equipment operations.