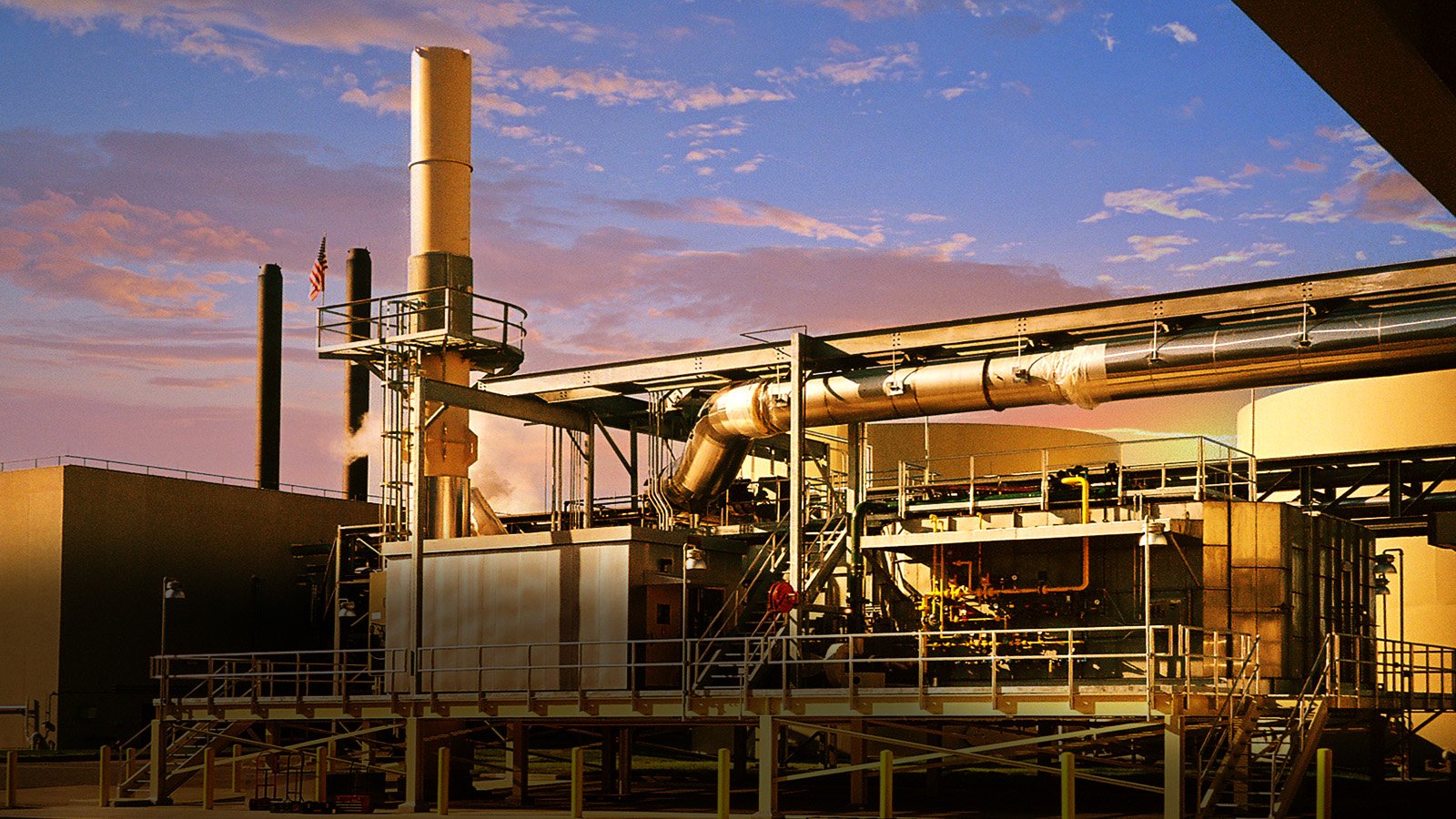
EPCON Integrated Systems
Multistage Heat Recovery Solutions

Product Overview
Multistage Heat Recovery Methods
Multistage Heat recovery in an integrated solution can create a closed loop system and is the best way to maximize your process efficiencies. By extracting and recycling the thermal energy at various stages in the process, heat recovery not only saves on operating cost but also fuel efficiency. Based on the unique process and requirements, different types of heat exchangers can be integrated into the overall system. Epcon hold several patents in the field of heat recovery and our team of experienced engineers can advise of the many opportunities to best utilize primary, secondary and even tertiary heat recovery methods into your process operations.
Primary Heat Exchange Systems
Primary Heat exchangers are heat exchangers which use the recently combusted hot gas to pre-heat the process gas entering the Oxidizer. These kinds of heat recovery systems save energy costs by reducing the amount of fuel required to maintain combustion. There are two main kinds of Primary heat exchangers:
Recuperative systems, which are generally air-to-air exchange systems which heat the process gas through a shell and tube system, which directly heats the air through convection, these systems can have heat recovery effectiveness of approximately 80%. These systems rely on a shell and tube type heat exchanger, where the hotter gas passes over the shell, heating up the cool gas passing through the tubes, using convection. Shell and tube type of heat exchangers are further divided on the basis of their operation. In parallel type heat exchangers, cold gas which is required to be heated passes through tubes, which are arranged in several passes. Hot gases flow on the shell side of the heat exchanger in a straight line. Another heat exchanger is counter type of heat exchanger, where the hot gases incoming the heat exchanger come in contact with cold gases leaving the heat exchanger. Conversely, hot gases entering the system, which have the highest temperature in the system, heat up the cold gases which are already heated up. Counter type of heat exchangers give the highest efficiency for heat exchangers. Majority of heat exchangers used at Epcon fall into this category. In series type heat exchangers, hot gases coming out of the thermal oxidizer pass through tubes and cold gases pass on the shell side. A number of passes are arranged on the shell side for the cold gases to pass over much larger area of tubes. The hot gases pass through the tubes, which are arranged longitudinally.
Regenerative systems, which uses a ceramic media to conduct the heat from the hot gas to the process gas, these systems can have heat recovery effectiveness of up to 95%.
The process gas is brought through the pre-heated ceramic bed and is combusted. After an allotted time the valves are closed and the process gas flows out over another ceramic bed, which is subsequently heated, thus pre-heating the gas, combusted and flows over another ceramic bed. Two or three ceramic beds alternate the duty of pre-heating and being heated, as their valves are opened and closed.
As compared to Recuperative systems, Regenerative systems are not steady state, rather they rely on a cycling gas which flows between at least two fixed packed beds. In this case, at least one bed would be an inlet, while the other would be an outlet bed. A common combustion/retention chamber connects the two. These vessels are connected by inlet and outlet control valves to direct air flow through the different beds. The hot air from the combustion chamber would flow through one of the beds, heating it up, while the other discharges, then cold process air would flow through the heated ceramic, reaching near the temperature needed for combustion. Then after being combusted, would flow through the cold ceramic again to heat it back up. This would be a continuous cycle of retention and purging. Continued preheating of the process gas causes the ceramic media canister to cool down, at the same time the ceramic media in the next chamber is heated. The inherent nature of the Regenerative Systems involves discontinuous or cyclic operation.
Secondary Heat Exchange Systems
Secondary heat exchange systems use the hot gas from the combustion process to run other processes within the manufacturing facility. There are many different applications for secondary systems. At Epcon we have produced many of these. The most commonly used are Thermal Flued Heaters such as waste heat hot water heaters and boilers, which can be used to heat water for washers, or heating systems within the factory. Another use is process heating, where the air can be used for systems like ovens or other curing devices. These systems are custom, but the general idea remains the same. The gas leaving the oxidizer will generally heat a pre-heat exchanger, then it will continue to the secondary exchanger. The secondary exchanger will use this heat in a manner specified to the particular device, and then will release the air to the atmosphere.
Tertiary Heat Exchange Systems
When applicable a third phase of heat recovery can be integrated into the system to further enhance the thermal efficiency. Tertiary heat exchangers typically recover heat that would be released after the secondary heat exchanger and recycle that thermal energy to propel other mechanical forces of the facility operations, such as compress vapors or pump liquids or move turbines that generate electricity. Additionally, tertiary heat recovery methods can be utilized for general comfort heating throughout a facility.
Integrated Systems Quick Links:
Multistage Heat Recovery Solutions