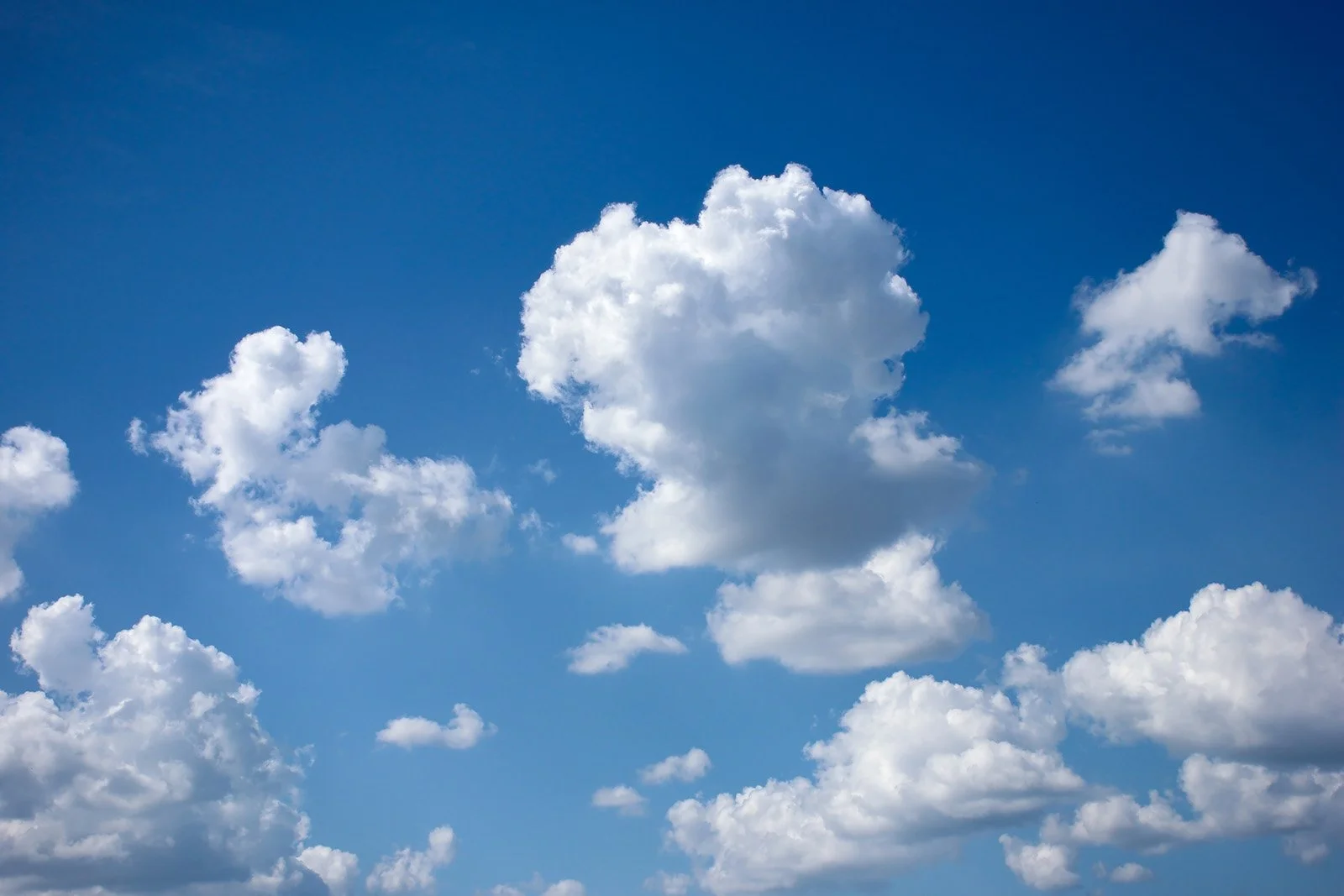
EPCON Air Pollution Control Systems
Recuperative Thermal Oxidizer

Product Overview
Recuperative Thermal Oxidizer
Epcon is an industry leader in Thermal Oxidizer technology specializing in the integration of customers’ process heating operations together with their Thermal Oxidizer requirements. In simple terms, a recuperative thermal oxidizer is the evolution of the direct fired thermal oxidizer through the addition of primary and/or secondary heat recovery.
Addition of heat recovery to the oxidation process can provide tremendous cost savings with respect to minimizing the use of natural gas for the air pollution control application as well as external process heat loads.
Primary heat recovery is accomplished when you direct the process exhaust vent stream through a heat exchanger, which crosses the outlet of the oxidizer exhaust, prior to inlet to the oxidizer. This results in recovering (recuperating) heat from the exhaust to pre-heat the air entering the combustion chamber reducing the thermal load and therefore gas consumption to achieve oxidation temperatures.
Secondary heat recovery is accomplished when you utilize waste heat from the oxidizer to support a secondary process (e.g. Oven, Washline, etc). This is accomplished by directing either fresh air or process air through a heat exchanger, which crosses the outlet of the oxidizer exhaust, and sending it to a secondary process. The recovered (recuperated) heat from the exhaust is often sufficient to support entire drying or curing operations. In many cases, energy saved with the addition of secondary heat recovery can offer paybacks in close to one year.
Epcon’s proprietary Recuperative Thermal Oxidizers are fabricated from select Stainless Steel Alloys to meet the process and duty cycle requirements for a given project.
Epcon’s Recuperative Thermal Oxidizers typically operate at 1400°F, with a residence time of 1 second and a heat recovery efficiency of up to 80%. Turbulent flow allows these systems to achieve such high destruction efficiency, up to 99.99% and high heat recovery as well. Higher operating temperatures are also achievable for hard to oxidize chlorinated compounds. Epcon also offers recuperative systems with catalytic modules suitable for VOC destruction.
The Recuperative Thermal Oxidizer is a thermal oxidizing system consisting of a combustion chamber with a shell and tube heat pre-heat exchanger. The high levels of destruction efficiency are achieved by the design of the system giving equal importance to three oxidation parameters:
1.) Temperature
2.) Time
3.) Turbulence
Epcon’s proprietary Tube and Shell Heat Exchangers are fabricated from select stainless steel alloys at our vertically integrated 250,000 Sq Ft manufacturing operations in The Woodlands, TX.
Processes that may benefit from Epcon’s abatement technology include the following operations:
Coating Operations
Chlorinated and Fluorinated Vent Streams
Curing Ovens
Fired Heaters and Boilers
Gas Turbine Engines
H2S Abatement
Oil Refineries
Paint Finishing Systems
Priming Operations
Soil Remediation Oxidizers
Stationary Engines
Wastewater Purification
Waste Gas Treatment
Air Pollution Control Systems Quick Links:
Recuperative Thermal Oxidizer