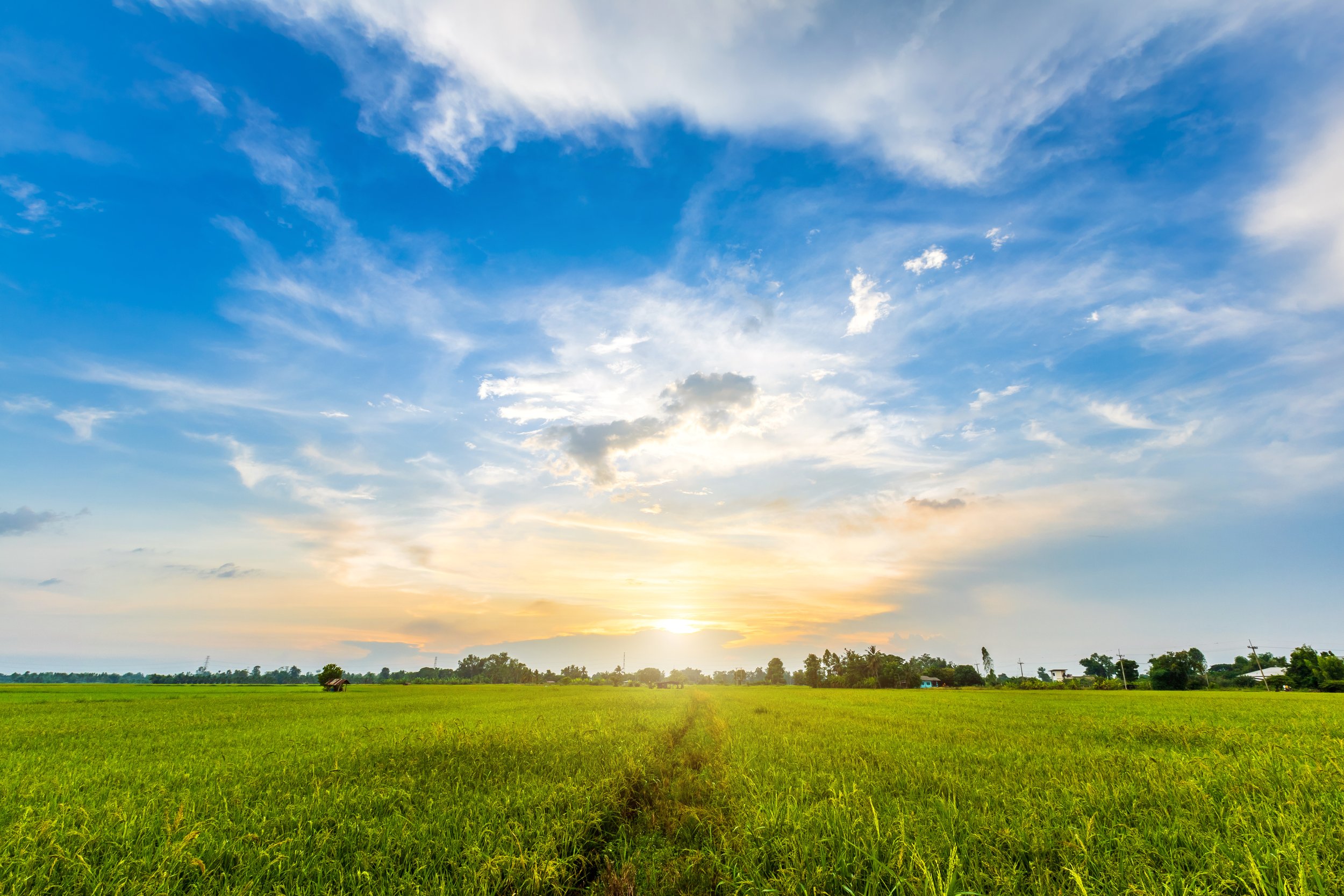
Patent 4322203
Industrial Pipe Burnout Oven With Pollution Control
This patent was developed for the pipe coating industry for a major pipe coater, and represents air pollution compliance and unprecedented heat recovery for maximizing fuel savings. This pioneering technology, for the Pipe Burnout Oven revolutionized the Pipe Coating industry around the world.
The oven is provided with a pair of oppositely positioned plenums along the sides thereof which supply heated air in large volume and high velocity through a plurality of nozzle slots to the pipe-containing chamber and are themselves supplied from a recirculation burner chamber on the top of the oven. A relatively small volume of air, laden with volatile, combustible fumes, is withdrawn from the oven at a relatively low velocity by an exhaust fan. This fume-laden air is passed through a gas-fired incinerator in a combustion chamber where the fumes are completely burned and the combustion products raised to a temperature of about 1400.degree. F. These combustion products are passed through a heat exchanger in the burner chamber on top of the oven and then through another heat exchanger to preheat combustion air for the gas-fired burners prior to being exhausted to atmosphere.
Drill Pipe is used over and over again, meaning, once the drilling operation is over. The pipe is refurbished in the Burnout Oven, and recoated for reuse.
A batch type Burnout Oven, is used for pre-coated dirty pipe filled with paraffin, wax, grease and old coatings. This patent pertains to the heat recovery within the Burnout Oven, utilizing Primary, Secondary, and Tertiary Heat Exchangers.
In terms of the efficiency, time savings, and the volume of pipes capable of being processed simultaneously, this patented technology propelled the pipe coating industry.
Epcon used this patent to build multiple pipe coating plants around the world, and still utilizes the application of this patent in its entirety and parts thereof.